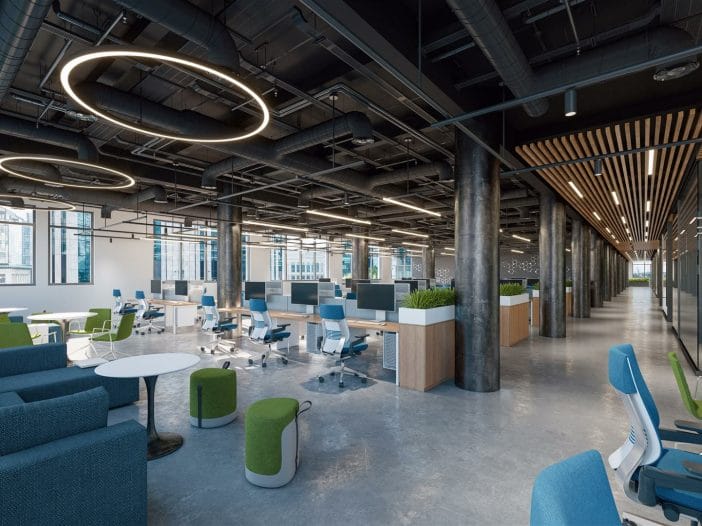
ROI
ROI
Commercial Observer
SGA – a national firm whose work spans architecture, interior design, planning, branded environments, and virtual design and construction – has a proven track record of delivering tech-forward design and state-of-the-art facilities for a number of clients. With 11 million square feet of active life sciences projects and nearly a dozen completed buildings and campuses under their belt, they are especially adept in the design of life sciences spaces, which has earned them a spot on Fast Company’s Most Innovative Companies list and the honor of Life Sciences Design Firm of the Year from Boston Real Estate Times.
Every year Fast Company editors compile lists that celebrate the world’s most innovative companies who are pioneers in their fields. This year SGA was named as one of the top 10 architecture firms for future-proofing life sciences buildings for any new scientific challenges. According to Fast Company, “SGA’s approach to architecture has become vital in the age of the pandemic. In the designs it’s created over the past year for more than 4 million square feet of new life science facilities in Greater Boston, SGA has applied some of the lessons of the pandemic to create spaces with movable cabinetry and modular mechanical systems where researchers and scientists can quickly adapt to changing conditions and global needs – buildings that are ready for whatever scientific challenges lie ahead.”
Another significant accomplishment for the firm this year is being named Life Sciences Design Firm of the Year by Boston Real Estate Times. “SGA has become a go-to firm when it comes to designing Class-A Life Sciences facilities for developers, owners and users throughout North America, with their designs behind four million square feet of Greater Boston’s new life sciences facilities in the last couple of years alone,” said Upendra Mishra, publisher of Boston Real Estate Times and Life Sciences Times.
SGA is at the forefront of its field in the specialized programming, planning, and design of research and development facilities for life sciences. It is an industry leader in life sciences facilities design, having cultivated a deep understanding of the critical metrics and capacities necessary to provide a flexible and efficient life science core and shell environment. Some notable life sciences facilities designed by SGA include:
By: Matthew Fickett AIA, LEED, CPHC | Principal
In Part 1 of this series, we discussed why 2 CFM/SF is the wrong metric for lab ventilation, and costs you twice as much as you need to spend. In Part 2, we showed that an efficient laboratory ventilation system doesn’t compromise your ability to provide for fume hood usage. In this part, we’ll discuss another big driver of lab ventilation: vivariums.
Ventilation in Vivariums
Recall that the commonly-used standard for lab ventilation is to replace the air once every ten minutes, or 6 Air Changes per Hour (6 ACH). It is generally agreed that vivariums benefit from greater air change rates. In general, 10-15 ACH is commonly used for small animal vivariums. Giving a range that wide may seem like I’m avoiding the question, but let’s look at an example.
The NIH requires 10 ACH for holding rooms (where the animals live) provided that the animals are in ventilated cages: that is, the cages are mounted on racks, like books on a shelf, and each cage gets its own individual feed for fresh air and exhaust air, from the rack. The rack works much like a fume hood, in that it pulls air from the room, uses it, and then exhausts it through a duct to the lab exhaust system. It also has very much the same goals: preventing air from the animals from getting into the room at large.
How much?
A very large cage rack (a double-sided one which holds nearly 200 cages) might use 150 CFM. Can we use the same method we did for fume hoods, and depend on that “background” 10 ACH ventilation to provide for the cage rack?
Although cage racks are kept in small holding rooms, the room is hardly ever just cage racks. There is a sink, a safety shower, a transfer station, and other equipment, plus some open space to move around in with bulky wheeled carts and racks. A 130 SF holding room might contain one double-sided rack as described above, plus a single-sided one, for a total draw of 150 + 75 = 225 CFM. That same room, if it has a 9’-0” ceiling, is 1170 cubic feet, which must be provided with 195 CFM of air to achieve 10 ACH. So, unfortunately we can’t just depend on background ventilation for this room!
To meet that 225 CFM draw, we have to provide the room with 11.5 air changes per hour (ACH). That’s not far off the mid-point of the 10-15 ACH range.
Big Picture Vivarium Planning
You might be saying to yourself, that’s all very well for one specific holding room, but all I know is that I want to provide for one whole floor to be a vivarium. How big does my air handler (and my shaft ductwork) need to be?
You can work through examples for other room types, and find values in the same range. There are some rooms (e.g. necropsy) where 15 ACH is required, and some rooms (e.g. the corridor) where nothing will push you above 10 ACH in any case. In general you’ll find that for rodent facilities, splitting the difference, and providing 13 ACH for the whole footprint of the vivarium, will be enough.
Coming back to our original terminology, 13 ACH in a 9’-0” ceiling space is 1.95 CFM/SF. So even high-level space like vivariums can be accommodated in less than the original 2 CFM/SF!
Conclusion
For normal lab space, even labs with a lot of fume hoods, 2 CFM/SF is more than twice as much air as you need.
For high-ventilation spaces like vivariums, which need an average of 13 ACH, 2 CFM/SF is still more than needed – but just by a little bit.
If you are planning a whole building, and expect that perhaps 10% of the lab will be a vivarium, you can size your equipment based on the average:
0.9 x 6 ACH + 0.1 x 13 ACH = 6.7 ACH
Or, if it’s easier in CFM/SF, a 9-foot ceiling would make that just plain 1.0 CFM/SF. So save money on capital costs and energy bills, check your ceiling heights, and cut that 2 CFM/SF in half.
By: Matthew Fickett AIA, LEED, CPHC | Principal
Part 1 of this series showed that 2 CFM/SF doesn’t measure lab ventilation the right way, and also usually provides more than twice as much air as we need. In this part, we’ll discuss one main factor in lab ventilation: fume hoods.
What for?
Scientists use all kinds of chemicals and organisms which can be harmful to people in their work, and the first priority of lab design is keeping people safe from all these hazards. We talk about this safety in levels of containment:
Fume hoods are an example of secondary containment.
How do fume hoods work?
A fume hood pulls air from the rest of the lab in through the open front, then sends it up an exhaust duct. This lets a scientist reach in through the open front of the hood to do work, but ensures that there’s no chance they will breathe any contaminated air. To put it another way: the main job of a fume hood is to ensure that once any air has gone in the front, it never comes back out the same way.
Older fume hoods do this in a sort of brute-force way: just move enough air, and you can be sure none is going the other direction! Modern fume hoods are designed to carefully manage the airflow, so that a much smaller amount of air movement still provides the same safety.
Different fume hoods use different amounts of air to create a safe environment, but a very conservative upper limit is 700 CFM (Cubic Feet per Minute) for a 6’ wide fume hood. It could easily be less than a third of that!
Where does it come from?
A common mistake is to imagine that the air a fume hood needs is extra, in addition to the 6 ACH (Air Changes per Hour) that the lab requires. Actually, you can use the same air for both. This isn’t a compromise in safety; it’s correct design. Let’s break it down.
Remember that the standard, 6 ACH, is air changes per hour. That is, new air arrives, and the old air leaves. So, for every bit of air in the lab, it must get removed (somehow) and replaced (somehow). In a lab by itself, there’s a duct delivering air through a supply diffuser in the ceiling, and a different duct removing that same air through an exhaust grille in the ceiling.
Recall that fume hood is taking air from the lab, and sending it up a duct to the lab exhaust system. Therefore, if you add a fume hood to the lab, all you have done is add another way for air to leave the lab. You can think of a fume hood as just a very complicated-looking exhaust grille. There’s no change to the total amount of air being moved through the lab; it’s just that some of it leaves through a normal exhaust grille, and some of it leaves through the fume hood.
How many hoods can you have?
Consider our worst-case example, a 700 CFM hood. Remember that in Part 1, we discussed how a 6 ACH target means that in a typical 9’-0” tall lab space, you are getting 0.9 CFM/SF. 700 CFM divided by 0.9 CFM/SF tells us that for every 778 square feet of lab, we are already getting enough clean air to supply the fume hood.
To put it another way, you can have one fume hood per 778 square feet of lab space, without needing any extra air at all. If you used a higher-efficiency fume hood, one which only needs 250 CFM, you could have one fume hood per every 278 square feet of lab space.
What else?
In part 3, we will look at vivariums.
By: Matthew Fickett AIA, LEED, CPHC | Principal
What’s the purpose of lab ventilation?
Science is inherently dangerous. Scientists use chemicals that dissolve other things (solvents and acids), chemicals that burn (sometimes all by themselves), or chemicals that are poisonous to humans. Scientists also work with organisms that cause diseases, sometimes for which we have no cure. There are safety procedures for all these things, but to ensure no leak or accident presents a danger, labs are designed to keep people safe in multiple ways.
One major way labs keep people safe is to provide a lot of fresh air, and to constantly remove the air inside the lab, in case it has become contaminated by something. It is commonly accepted that air in standard bench labs should be replaced every 10 minutes. Another way to say this is 6 Air Changes per Hour, or 6 ACH.
As simple as that?
Of course not! It is important to note that this 6 ACH figure is not universally accepted, and is not written in the building code. There are many standards which discuss lab ventilation, including:
None of these standards gives a single, universal number. All of them argue that the correct ventilation is different for every situation. However, as designers and building owners, we often have to design the mechanical systems for a building before you know exactly what sort of lab will be inside it. We have to pick some number! 6 ACH is a good minimum for now. It’s possible to go lower, but you definitely don’t need to go higher in a normal bench lab. (In addition, many institutions, including the NIH, specifically name 6 ACH. If you’re curious for more, the NIH Design Requirement Manual is a good place to start.)
ACH versus CFM
You’ll often hear discussion of CFM/SF (cubic feet per minute, per square foot). This gives each square foot of the floor of a building a certain amount of ventilation – often two cubic feet of fresh air every minute.
Let’s compare this number to 6 ACH.
Table 1: Comparison of Lab Ventilation Rates for a 9’-0” ceiling height
Benchmark | 6 ACH | 2 CFM/SF |
Air Changes per Hour (ACH) | 6.0 | 13.3 |
Cubic Feet per Minute per Square Foot (CFM/SF) | 0.9 | 2.0 |
2 CFM/SF is more than twice as much air as 6 ACH! That means your air handlers are twice as big, your shafts take up twice as much space in your building, and you’re spending twice as much to condition that air.
What about fume hoods?
But wait, I hear you saying. What about fume hoods? Don’t they require tons of extra air? I don’t want to design a building which prevents scientists from using all the fume hoods they need.
You don’t have to! We’ll discuss this in Part 2 of this series.
Bisnow
The Boston Real Estate Times
Bisnow
Boston Real Estate Times
Boston Real Estate Times
SGA, a Boston and New York City-based national award-winning architecture, interior design, planning, branded environments and virtual design and construction practice, today announced that the New England Chapter of CoreNet Global has awarded the Best New Small Workplace Award to the SGA-designed 70,000-square-foot headquarters of Pipefitters Local 537 in Dorchester, MA.
The winners of New England CoreNet Global’s annual Awards of Excellence represent the best of the Boston region in corporate real estate leadership. Winners will be formally presented with their awards at the in-person Awards of Excellence Gala on October 28th, at the Westin Boston Seaport District hotel in Boston.
“Our goal was to have a timeless building that was both beautiful on the outside and functional on the inside,” said Brian Kelly, United Association’s Director of HVACR Services and former Business Manager/Financial Secretary-Treasurer of Pipefitters Local 537. “When people drive up just to look at the building, you just see the amazement in their eyes… SGA was one-stop shopping for us. They did everything from the design of the exterior, interior, and continue to work on some branding for us as well…they handled the entire project from start to finish.”
Pipefitter’s vision was to create a 100-year state-of-the-art training facility for their union members, which incorporated the latest technology as well as the flexibility to evolve with the times as their profession is ever progressing. The new building provides ample training space, brings all departments under one roof, and engages with the local community by strategically placing the welding shop along the glass façade at the front sidewalk and adding large-scale graphics and branding in the lobby.
The many specialty spaces at the building support their equipment, training, and classroom requirements, including an 8,000 s/f welding workshop complete with classrooms and high-tech lab spaces. The multi-use building also features an auditorium to accommodate over 500 union members.
“It’s truly an honor to receive this prestigious award from the New England chapter of CoreNet Global,” said Gable Clarke, IIDA, LEED® AP, Partner and Director of Interior Design at SGA. “We thank the jury and CoreNet for this honor and for recognizing this unique project.”
The Boston Globe
SGA has been retained by two global real estate developers, Lendlease and Ivanhoé Cambridge, to design a new Life Sciences building at 60 Guest Street in Boston Landing, in Allston/Brighton, MA.
For the project, a proposed nine-story structure that will offer 320,000-square-feet of the state-of-the-art lab and office space, SGA has designed an iconic building visible from the Massachusetts Turnpike that will easily hold its own among local landmarks such as New Balance’s Global Headquarters, the Boston Celtics’ Auerbach Center, and the Bruins’ Warrior Ice Arena.
SGA Partner and Director of Architecture John Sullivan, AIA, explains: “The exterior will feature curvilinear forms intended to give the building a sculpted look. It’s been designed with a reflective high-performance facade that is visually responsive to both the surrounding neighborhood and the nearby Mass Pike.”
Furthermore, Sullivan says, the planned building will be highly sustainable and will boast a robust amenities program, along with parking and plentiful outdoor spaces. “There will be terraces with views to both the Boston skyline and the Charles River and active retail along Guest Street.”
As designed, 60 Guest will be an important addition to both the vibrant, mixed-use neighborhood of Boston Landing and to Allston/Brighton’s emerging Life Sciences cluster. “Due in part to its proximity to Kendall Square, this area has seen robust demand for specialized Life Sciences and research facilities. We are excited to fulfill those needs with a new state-of-the-art, ultramodern Life Sciences building,” says Sullivan.
New England Real Estate Journal
BOSTON- SGA, a Boston and New York City-based national award-winning architecture, interior design, planning, branded environments and virtual design and construction practice, announced that after adding architects, designers and support staff in Boston and New York City, it has hit a milestone of reaching a team of over 100 people.
“It has always been a key mission at SGA to attract exceptional talent in the industry. The new additions to our growing team allow us to maintain a high level of service across all the sectors we work in,” said John Sullivan AIA, Partner and Director of Architecture at SGA. “We’re excited to welcome them all to the team at SGA.”
SGA’s latest hires are: Saida Akhmedova, Job Captain; Samantha Carson, IIDA, Interior Designer ;Siying Chen, Project Designer; Paul Clark, LEED AP, Project Designer; Kailey Domit, Interior Designer; Megan Dunn, NCARB, Project Designer ; Jennifer Kady, NCARB, CDT, AIA, Project Architect; Mike Lee, Senior Designer; Michael Sansevero, Interior Designer; Swati Sawhney, LEED AP BC+C, International Associate AIA, Project Designer; and Kun Zhang, LEED GA, NCARB, Associate AIA, Project Designer.
In addition to these new hires, SGA earlier added 10 architects and interior designers to its expanding teams in Boston and New York City: Dan Connolly, Project Architect; Brandon Dotson, LEED GA, Architecture Project Designer; Michael Epstein, Job Captain; Zach Fields, Junior Project Designer; Charles Hergrueter, AIA, NCARB, BSA, Project Designer; Gunner Kleinschmidt, AIA, Senior Project Manager; Amanda Lombardo, Interior Designer; Dorran Prescott, LEED AP, NCIDQ, Senior Project Manager; Corie Smith, NCIDQ, IIDA, Senior Interior Designer; and Elizabeth Yusem, LEED AP, BSA, AIA, Project Architect.
To learn more about SGA’s exceptional team of professionals, please visit click here.
Boston Business Journal
In Part 1 of this series, we defined Net Zero and discussed why a building must be all-electric. In Part 2, we discussed the lab-specific space conditioning and exhaust challenges related to safety and fume hoods. However, going Net-Zero has impacts beyond just lab air; we’ll discuss those here, in Part 3.
What effect does being all-electric have on building systems?
The visible impacts are surprisingly small. Some of the most important effects are behind the scenes: for example, no gas appliances mean less exhaust, so shaft sizes can be reduced. Similarly, heat-pump space conditioning means that you only move air around for ventilation, so for any spaces which were previously conditioned by blowing hot or cold air around, duct sizes (and shaft sizes) are reduced.
What about electrical infrastructure?
It’s normal to read all this about all-electric buildings and imagine upgrades to the electrical system, all the way to increasing the service size from the utility company. In fact, most all-electric buildings don’t need to increase electrical connection size at all. Why? Because most buildings already have all-electric cooling in the summer. Since cooling is (usually) a larger load than heating, the electrical connection the building has is already more than enough to handle the heating load in the winter.
But isn’t electricity more expensive?
Yes – but no. (It’s complicated.)
Yes, per unit of energy, it costs more to buy a unit of electricity than a unit of energy in the form of gas or oil. However, electrical building systems are so much more efficient than gas-fired ones that the price per unit of heat in the building is actually very close.
As I write this in 2021, the price to condition a building that is all-electric is somewhere around 10% more than the price to condition a building that’s a conventional gas/electric combination. However, the price of electricity has been quite steady over the last couple of decades, while the price of gas has varied quite a bit. It’s near a historic low now, but not very long ago, it was more than double the current price. So while electricity looks just a bit more expensive now, it would have been a much cheaper choice for many of the last 20 years and is likely to be cheaper again in the future.
What if you can’t predict the price of electricity? What if gas is cheap forever?
It’s certainly hard to predict the price of anything in the future. However, there’s a different financial consideration, which you have probably heard of under the name “carbon tax”. Put very simply, it’s a fine you pay for dumping smoke into the atmosphere. Think of it as a fine for littering.
While carbon taxes are just beginning to be implemented, they are growing rapidly, and it’s no surprise that science-friendly states and cities where so many labs are located are the same ones who are farthest ahead on passing these laws. In the future, it’s likely that even if gas is cheaper to buy, it will be more expensive to burn.
Doesn’t the utility company just burn gas (or coal) to make electricity anyway?
It’s true – most of the electricity generated today is created by burning fossil fuels. But that’s today: it’s changing rapidly. In my home state of Massachusetts, the portion of the grid powered by renewable sources is climbing 2 or 3% per year, just because it’s cheaper to build and operate. That growth is accelerating; it’s not hard to look ahead and see an all-renewable grid.
When that happens, an all-electric building powered by the grid will instantly be Net Zero, with no solar panels insight. In short: it’s possible to produce electricity in a Net Zero way; it will never be possible to burn gas in a Net Zero way.
What about emergency power?
If you’re wholly dependent on electricity, it’s important to have a good backup. Right now, battery technology has come a long way: not just in electric cars, but even utility companies are building giant battery farms to provide grid-scale backup during blackouts. It’s entirely realistic to talk about building-scale battery backup.
Still, some science requires the kind of peace of mind that comes from a backup system that is completely separate. In those cases, building a natural gas generator is not a bad solution. Yes, it sounds like it undermines everything I’ve writing in this series: burning natural gas in a Net Zero building! But if a building is all-electric except for one or two days per year when the power is out, that’s 99.5% Net Zero operation. If we reduce our pollution by 99.5%, I’d call that a very good accomplishment.
Bisnow
SGA, a Boston and New York City-based national award-winning architecture, interior design, planning, branded environments and virtual design and construction practice, today announced that the company has received a Special Mention in the category “Architecture+Preservation” in the 9th Annual Architizer A+Awards for their work on Peabody College of Education and Human Development at Vanderbilt University in Nashville, TN.
The Special Mention in the “Architecture+Preservation” category recognizes works that preserve and enhance their existing built environment.
In partnership with Centric Architecture in 2020, SGA’s higher education group led the process as Design Architect on 71,000 square feet of renovations and additions for Peabody College at Vanderbilt University.
Included in the 71,000 square feet of renovations and additions was a “jewel box” connector addition that serves as a new student center for graduate programs and active learning classrooms, fulfilling Peabody College’s wish to create a new school center. The redesign split the boxy building in two; replacing the concrete walls with glass which added depth to the façade and created a light-filled atrium lobby with café and lounge.
“We are honored to receive this Special Mention from the Architizer A+Awards,” said David Enriquez, LEED AP BD+C, Architect and Senior Designer at SGA. “The preservation of existing buildings and space in any design requires a unique architectural disposition and a specialized skill-set, and we are pleased to have our efforts in the Peabody College project recognized by such a well-known publication.”
In addition to Architizer A+Awards, SGA’s design at Peabody College previously received an Honor Award at the AIA Middle Tennessee 2020 Design Awards. In 2020, SGA received about a dozen awards for its pioneering design and architectural work.
By: Matthew Fickett AIA, CPHC, LEED
Principal
What does this mean for labs?
In Part 1 of this series, we discussed what makes a building Net Zero, why a Net Zero building must be all-electric, and a key piece of technology which allows efficient, cost-effective electric space conditioning: the heat pump. But what about laboratory buildings? Don’t they have all kinds of special needs?
Space conditioning, the lab version
In fact, the biggest energy draw in a lab building is space conditioning, just like it is in most buildings. The difference is that in a lab building, it is often five or ten times more than in other building types! The reason is rooted in safety: many science processes are dangerous to people, and to protect the scientists from their work, the air in the room is completely replaced every few minutes (commonly, six times per hour). Even more significantly, much of the work in a lab is done inside fume hoods, which pull in air from the lab and may exhaust it directly outside. This keeps scientists in the lab safe but requires the building to spend enormous amounts of energy conditioning fresh air, only to immediately throw it away.
The first step is simple: reduce the number of fume hoods (by reducing the number of hoods just used for storage and by encouraging sharing of hoods where possible) and then reduce the amount of air that goes through them. Modern hoods are far more air-efficient than older ones, while being safer than ever. Better engineered airflow, automatically closing sashes, variable air volume (VAV) controls, and occupancy sensors all work together to cut air use by half or more.
The second step is slightly more complicated: capture heat from outgoing exhaust air. This is already common in ordinary exhaust from, say, office space. There are a variety of technologies, but the principle of them all is the same: capture the warmth out of the exhaust and put it back into incoming air, before the building heats the air up. (Or, of course, the reverse in the summer.) This is not commonly applied to lab exhaust, but there’s no safety reason which would prevent it.
The last step is the most difficult: get rid of the fume hood exhaust altogether. Hoods without exhaust, called “ductless” or “recirculating” fume hoods, just run the exhaust through very high-grade filters before releasing it back into the lab. This may sound scary, but think about it: if the lab exhaust is dangerous to breathe, should we be releasing it out into the world anyway? It would be far better to treat it until it is safe, and once that’s done, you might as well get the benefit of keeping the heat energy inside the building.
Can we really do science in filtered fume hoods?
A filter for a fume hood is, of course, more complicated than your average air filter. The filter set has to be selected for the chemicals or processes to be used in the hood. It’s easy to imagine a strong acid used with the wrong filter which just melts the filter. This makes it sound like a daunting prospect, but it’s not as difficult as it sounds to get it right.
Most lab processes are fairly well known in advance. There are already many rules about what chemicals can or can’t be put down the drain, or how hazardous waste must be disposed of, or what tools and surfaces are compatible with which work. It’s actually quite unusual that we say “go ahead, put anything you like into the atmosphere, don’t worry about it!” Instead, a lab can be designed where certain hoods are used for certain tasks.
For the tasks you really can’t know in advance, like some R&D processes, one or two fume hoods could still exhaust to the outside. It would be better to get rid of them completely, but if 90% of the hoods in the building can be filtered, that’s still a great improvement.
What else?
That’s great for fume hoods, but there’s so much else to a lab! What does going all-electric, Net Zero do to the rest of the project? We’ll discuss that in Part 3 of this series.
Boston
99 High Street
Floor 4
Boston, MA 02110
(857) 300-2610
New York
18 W 18th Street
Floor 2
New York, NY 10011
(857) 300-2615
© SGA